Almak Ateş Makina
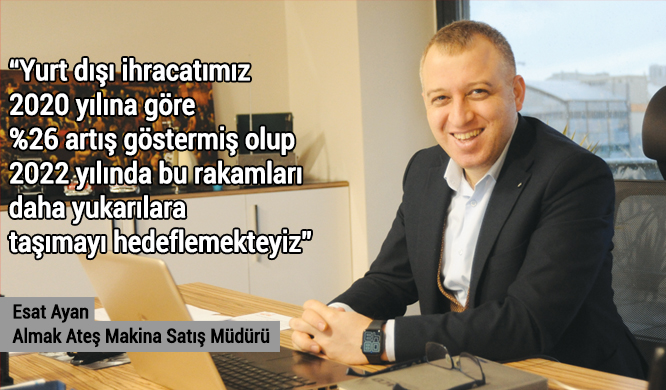
Breaking new ground in the screw barrel industry, Almak Ateş maintains steady growth by producing an average of 3000 screw barrels per year. We spoke to Almak Ateş Makina Sales Manager Esat Ayan about the production work, goals and sector issues of Turkey’s first screw and barrel facility with half a century of experience.
Can you tell us about the structure of your company and your position in the sector?
Our company was founded in 1968 by Ali Ateş, who is considered a veteran of our sector. Since our establishment we have become Turkey’s largest integrated screw barrel manufacturer with our many years of experience and as a result of technological endeavors. We have 95 employees in our company. We are taking firm steps towards our growth targets with our corporate identity and the devoted work of our teammates in our company, which has a total indoor area of 10,000 m². We follow all the innovations in our operations related to plasticization equipment, attach importance to R&D studies and follow all technological activities in this regard. The products we produce are used in all processing machines that are used in the appliance, automotive, cable industries and the construction, agriculture, textile and many other sectors. Companies that manufacture pipe and cables machines related to our sector comprise 50% of our customer portfolio. Our export abroad has increased by 26% compared to 2020 and we aim to take these figures even higher in 2022.
What has the Almak company brought to our country and what are the features that distinguish you from your competitors?
We, as Almak, have always focused on developing and improving our production line. We have never indexed our goals to a final point but as a result of the investments we have made always looking forward, we are deservedly proud to have contributed to our country in terms of added value. Our greatest difference that distinguishes us from our competitors is our 20 years of experience in nitration heat treatment and having a bimetallic barrel production line for 3 years. You can do the machining of a screw barrel very well, but if you do not have a good grasp on metallurgy, the life of the manufactured screw barrels will not be at the desired level. Accordingly, Almak provides services to its customers in a much more professional manner with the metallurgy laboratory in its structure and metallurgy engineers. All operations are carried out within our own structure, without outsourcing, from the moment we receive the unprocessed raw material for our customer’s order until it is transformed to the final screw barrel product to be delivered to the customer. By handling of the manufacturing work within its own structure, the Almak company continues to lead the sector. By performing all our manufacturing processes within our company as a result of our R&D studies and investments, we believe that we have added value to our country in many ways.
Can you tell us about the production process in your factory?
The manufacturing process in our factory is managed with the ERP (Almak Intelligence) system. This system we use in the manufacturing process, which begins in line with the demands of our customers, allows all processes to be implemented quickly and efficiently. From selecting the materials to the technical drawings, from the technical drawings to quality control; all processes from the moment the material enters until it is dispatched are controlled through this system. Thanks to this system, which operates in coordination with all our work stations, our operators, sales department, quality control and other departments maintain communication at the production stage. We are able to manage the process with a single system. With the barcode system our personnel working in the machine parks are able to track the whole process using tablets.
What machines are in your manufacturing park and what are your new investments?
In our manufacturing park we have CNC controlled lathe stations, CNC controlled screw opening stations, CNC honing stations and universal workstations. In the second half of 2021, we commissioned our 5 axis millturn turning center. With this station we are able to do both the lathe and milling work of a piece at one go without removing it at all. Thus we have made important progress for industry 4.0. Almak has distinct features far ahead of its rivals in terms of workstations because we partner with the best brands of the world in this sector.
What have you gained in 2021, what are your expectations for 2022?
Contrary to expectations, 2021 has been a very productive year for our company. Compared to the previous years, we achieved a growth in the 20-30% range with the effect of increasing in our export rate. In parallel with the increase in work, we also had the opportunity to expand our production line in terms of both workstations and employment. While our export rates increased, we also had the opportunity to reach out to new customers in the domestic market. This enabled us also to achieve growth acceleration in the domestic market. In line with the budget and manufacturing plans done at the end of the year, we plan to add even more to the previous years and increase our growth in 2022.